3分鐘內可製造三分之一的車體!豐田汽車展示新一體式壓鑄技術
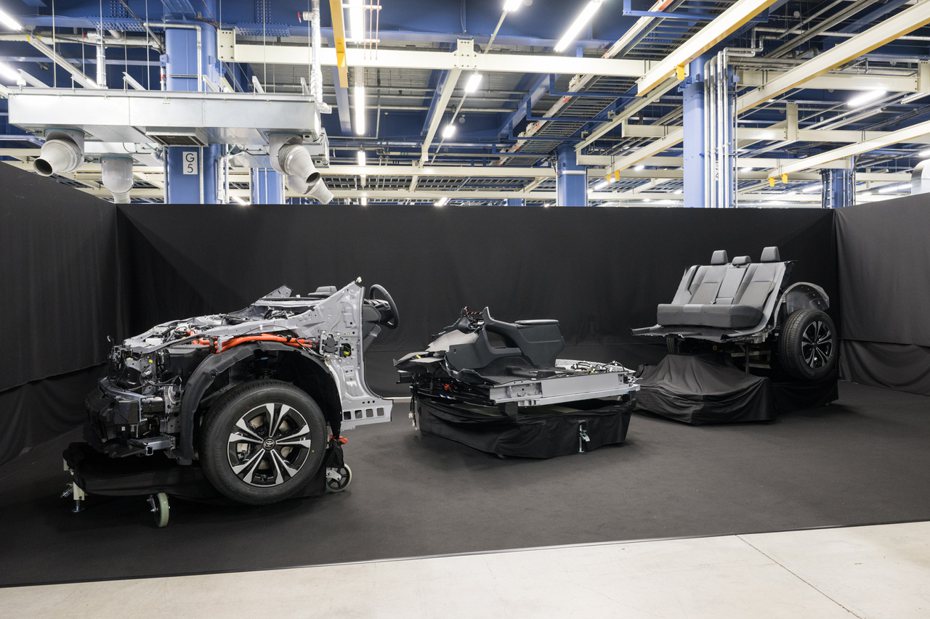
豐田汽車展示了新的一體式壓鑄(gigacasting)設備的原型,這種設備可在大約三分鐘內製造出三分之一的車體,這一發展將是豐田未來幾年提升電動車生產獲利計畫的關鍵。
日經新聞報導,豐田近期在明知廠把這款設備展現給記者看時,運作過程中冒出一陣白煙,熔化的鋁被倒入時,迅速從攝氏700度降至250度,凝固成單一壓鑄的部件,構成車輛底盤的整個後三分之一。目前,這一部分通常是透過33個步驟組裝86個零件,歷經數小時作業而成。
豐田目標利用這類進步的做法來縮減製造過程、廠房投資與製造的準備前置期,希望有助於在2030年前達成年銷350萬輛電動車的目標。
到2026年,一體式壓鑄技術將被用於生產一款新車的前端與後端部分。雖然這種重型模具起初需要長達一天的時間才能進行替換,但後來藉由減少需要拆線的零件數量,已把這一過程縮短至20分鐘。豐田的目標是透過專有軟體分析最佳的鑄造條件,達成比競爭同業高出20%的生產力。

豐田另一項策略則是自動化生產,更有效地利用工廠空間,以便與電動車生產所需的新設備配合。
在豐田汽車的元町廠,一輛配備有輪胎、電池,但尚無車身側面和車頂的半成品汽車以每秒0.1公尺的速度自動駛往一座機器手臂,機器手臂接著把一輛自動引導車輛運來的座椅安裝上。完成後,車輛移往至不同的區域進行檢查和出貨。
這種配置捨棄傳送帶,使工廠能更快速調整作業配置並減少投資。豐田的目標是讓組裝時間從現在的約10小時縮減一半。

由於電池成本高昂,若只是靠擴大傳統製造方式,電動車的生產是難以獲利的。特斯拉已經採用一體式壓鑄技術,藉由大量生產少少幾款車款的方式,來維持成本競爭力。然而,豐田擁有的汽車製造技術和設備,再加上車款陣容廣泛,使得豐田的狀況與成立才沒幾年的年輕公司不同。豐田生產長信吾和光表示:「我們正向專門的電動製造業者學習新的選項來應付挑戰。」
豐田目標2026年銷售150萬輛電動車,是去年銷量的約60倍。汽車業研究機構Nakanishi Research Institute執行長中西孝樹預期,40%左右的車會採用現有的豐田新全球架構平台製造,其餘則採用電動車專用平台。
豐田的傳統架構是設計用來平衡效率與舒適性,但預期在生產電動車時無法產生獲利。豐田預期在2030年目標銷售的350萬輛電動車中,約170萬輛是使用新的架構。豐田在2022年電動車銷量約2.4萬輛,遠遠不如特斯拉約131萬輛的交車數。

車訊最前線
延伸閱讀
最新文章

熱門新聞
